Engineering college fabricates free face shields for medical personnel
More than 2,100 face shields have been distributed to facilities in Middle Tennessee and beyond.
Janel Shoun-Smith | 615.966.7078 |
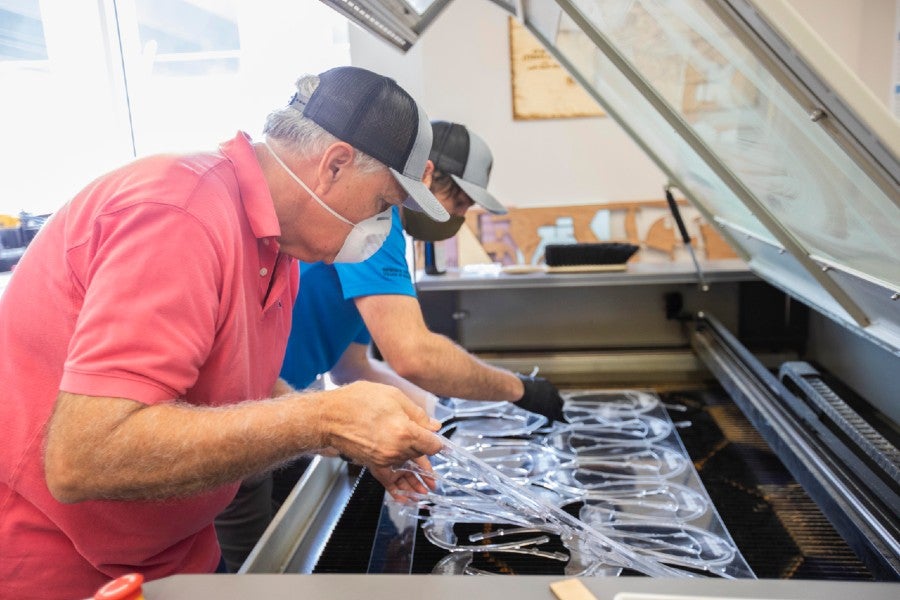
The directors of Lipscomb’s Peugeot Center for Engineering Service in Developing Communities are fabricating face shields, made from plastic, every day from Lipscomb's Fields Engineering Center.
In the News: WTVF-CBS NewsChannel5 WZTV-FOX17
*******
Lipscomb University's Raymond B. Jones College of Engineering is helping Middle Tennessee medical providers stay safe by fabricating and distributing protective face shields.
Face shields are personal protective equipment devices that are used by many medical workers for protection of the facial area from the body fluids of a patient. With production starting in the last week of March in Lipscomb’s Fields Engineering Center, they have produced more than 2,130 face shields so far.
Since March 28, more than 1,800 have been distributed free to more than 37 medical sites or individual health care workers in Davidson, Williamson and Maury counties including Southern Hills Medical Center, Williamson County Medical Center, Saint Thomas Medical Center and Nashville’s Siloam Health clinic for underinsured patients. Some have even been sent to New York.
The college updates the number produced each week on its COVID website here.
The directors of Lipscomb’s Peugeot Center for Engineering Service in Developing Communities, Steve Sherman, executive director, and Caleb Meeks, director of operations, along with Samuel Wright, the college’s engineering laboratory manager, are the core team producing the face shields, made from plastic. About five engineering students have volunteered to expand the crew in the coming weeks.
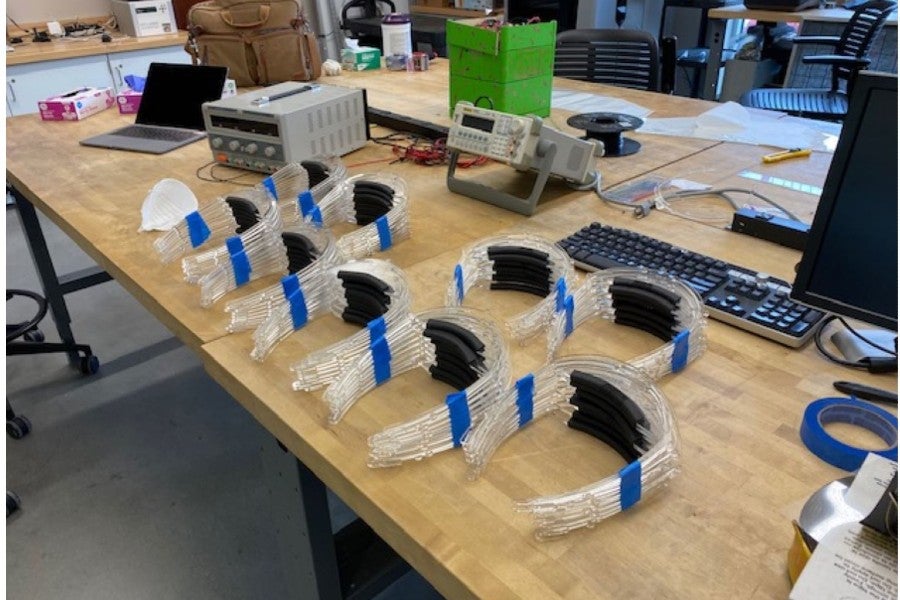
“We're using a high power, automated, laser system in our innovation lab to cut out the components,” said David Elrod, Dean of the College of Engineering.
In addition, Sherman and Meeks have created a video and downloadable instructions for making a wire-frame face shield out of off-the-shelf materials, a DIY face shield that health care workers in under-resourced nations can use for protection. The off-the-shelf version is made from 12-gauge wire and PVC vinyl--or in a pinch transparency sheets can be used--and a rubber band.
“We're using a high power, automated, laser system in our innovation lab to cut out the components,” said David Elrod, Dean of the College of Engineering. “Having the tools in the innovation lab lets us readily produce face shields to help local providers, and this second initiative is a way the Lipscomb team is helping folks without access to such unique tools in distant lands.”
READ MORE: Engineering partners with GM to 3D-print device to make medical masks more comfortable.
The Peugeot Center usually funds engineering students and professionals to complete engineering projects such as bridges, solar power systems, rain catchment systems and radio towers to benefit communities in disadvantaged nations around the world. As those international trips scheduled for spring and summer have now been canceled, the Peugeot Center is able to devote its resources to other engineering projects.
Meeks wears the wire-frame version made from off-the-shelf materials.
To produce the shields, Lipscomb engineering faculty reviewed existing proven designs and selected an open source design developed by the Georgia Institute of Technology’s engineering college. The team is following the CDC’s social distancing guidelines while manufacturing the shields, wearing gloves and masks as needed and limiting the team to two individuals working at a time, said Elrod.
Demand continues to grow. “We've had inquiries not only from medical providers and hospitals, but also from students who are requesting them for family members and loved ones who are on the frontlines of health care,” said Elrod.
“What you are doing is so so important and it makes me proud to be a Lipscomb engineering student,” said Lipscomb student Rachel Hohl, who obtained 30 face shields for CRNAs and anesthesiologists at her mother’s workplace. “I really wish I could be on campus to help out!"
“Connecting engineering capabilities with those in greatest need has been at the core of our engineering college and of the Peugeot Center. In this season, we are excited to find both virtual ways of staying connected with many of our international mission partners and to find new ways of serving our local communities,” he said.
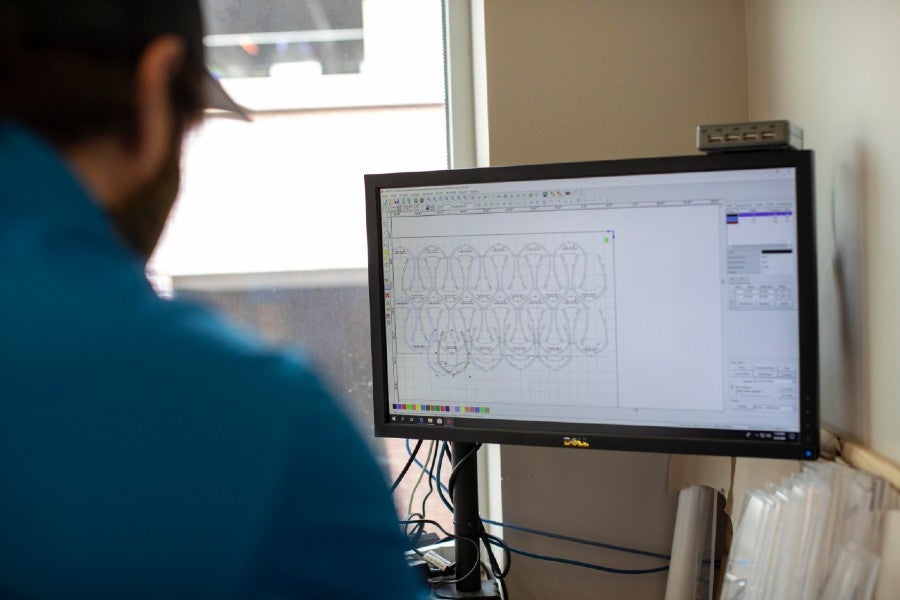
Using this visual template, the plastic headbands are cut from plastic by a laser etcher, housed in the College of Engineering innovation lab.
In addition to producing the face shields, Lipscomb’s engineering faculty and students are also working to complete design of a reproducible bio-incinerator for medical waste disposal for use in disadvantaged nations.
This senior design project was nearing completion in March as Lipscomb decided to move to remote instruction for the rest of the semester.
“By completing and testing it, we'll be able to send a validated design to medical facilities in Central America and Africa, which have traditionally relied on burn-pits to destroy contaminated materials,” Elrod said.
If you would like to receive some of the face shields crafted by the engineering college, contact Elrod at david.elrod [at] lipscomb.edu (subject: Request%20for%20Face%20Shields) (David[dot]Elrod[at]lipscomb[dot]edu).
Donate here to this special effort of the Peugeot Center for Engineering Service in Developing Communities.
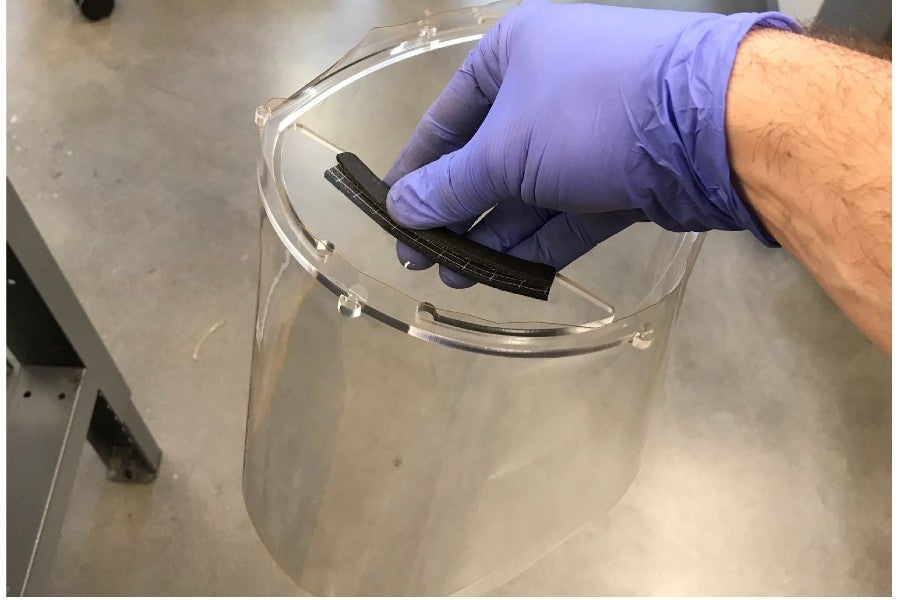
To produce the shields, Lipscomb engineering faculty reviewed existing proven designs and selected an open source design.